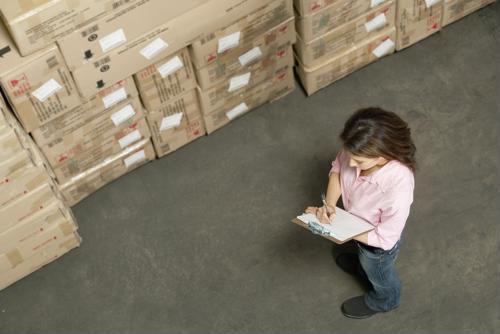
One of the most imperative pursuits in warehouse operations involves inventory management. Proper categorization and organization of available inventory translates to more efficient picking by warehouse employees, as well as streamlined order fulfillment for customers.
However, in many warehouses, inventory management remains a top challenge. There are certain common pain points that can come up with this important process. Thankfully, these three challenges can be avoided.
1) Improper item categorization
One issue that can throw off successful inventory management is a lack of clarity when it comes to merchandise categorization. Siloing specific items into their own distinct categories can help speed up the picking and fulfillment process. However, when a warehouse employee goes to a specific category in the warehouse to find an item, and realizes it is not where it's supposed to be, picking can quickly turn into a time-consuming wild goose chase.
In this way, it's imperative that inventory items are put into correct and logical categories, based on the unique products your business deals with.
"Defining moveable versus fixed assets is a broad categorization, but you should also categorize assets based on a system that makes sense for your company, whether that means categorizing assets by use case, by department, by value or some other metric," noted Camcode contributor Nicole Pontius.
"There's nothing worse than when inventory numbers don't line up."
2) Unclear inventory tracking
In addition to putting items into their own categories to support clarity for pickers, it's also important that warehouse stakeholders can properly track all inventory items. There's nothing worse for warehouse managers than when inventory numbers don't line up.
This issue is surprisingly common in ecommerce inventory management due to struggles with outdated, manual tracking methods, Retail Dive pointed out. After all, tracking items by hand can come with accidental, yet sometimes unavoidable human error that can result in inaccurate inventory counts. And any lost inventory translates to lost profits.
One of the best ways to avoid this issue is to update and streamline inventory tracking capabilities through an advanced order management system that comes equipped with product availability and allocation features, as well as inventory reduction capabilities. In this way, warehouse managers can always accurately see how much merchandise they have on hand, and these numbers are automatically updated every time an item is picked and scanned for order fulfillment.
3) Lack of organization for seasonal inventory
Seasonal items are something that nearly every business deals with, including things like holiday decorations or merchandise specifically for summer fun. When it comes time to stock and manage these items, however, a lack of organization can quickly create headaches.
Going back to our first pain point, proper categorization of these items is key, and it can be helpful to set aside specific space in the warehouse just for seasonal merchandise. After all, once summer inventory has been exhausted, it'll be time to stock back-to-school items, and Halloween inventory shortly thereafter.
This is also another area where an innovative OMS with product availability and allocation, as well as inventory reduction capabilities becomes a key asset. Such technology can eliminate these and other common pain points with inventory management, all the while supporting accuracy and insight into merchandise availability.
To find out more, check out our website and connect with us about our industry-leading FlexOMS today.